Для любой организации, использующей складские мощности, очень важно оптимизировать затраты на выполнение операций, сократить издержки и повысить производительность. Для этого компании стараются оперативно оценивать ситуацию на складе, формировать оптимальные маршруты движения персонала и подъемно- транспортного оборудования, эффективно выстраивать задания для сотрудников, а также проводить инвентаризацию, по возможности не останавливая работу склада. Помимо базовых, есть и более сложные задачи, реализация которых невозможна без применения специализированных информационных систем.
К числу наиболее ярких проектов, связанных с автоматизацией складского комплекса, можно отнести склад готовой продукции компании «САВА», одного из крупнейших мясокомбинатов в России. О «тонкостях» внедрения IT-систем на данном предприятии и особенностях этого процесса рассказал генеральный директор компании «ИСИТ» Алексей Николаевич Поваляев.
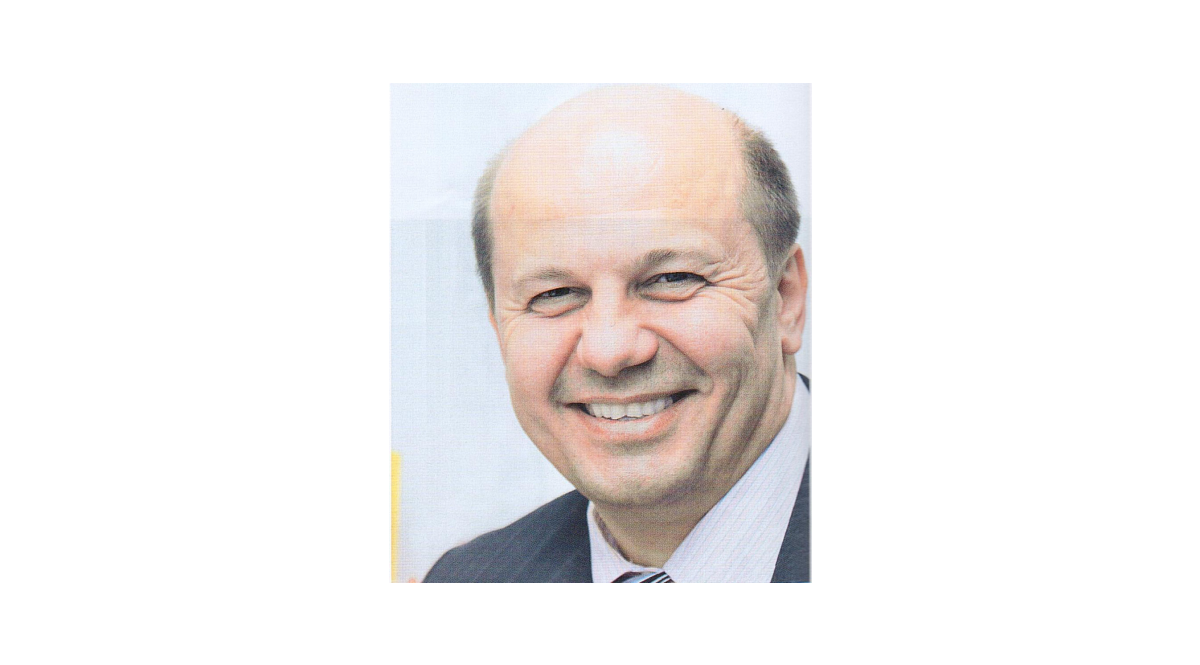
Алексей Николаевич, расскажите, пожалуйста, о недавнем проекте внедрения автоматизированной системы на мясокомбинате «САВА». В чем заключалась модернизация? Какие задачи приходилось решать в рамках проекта?
– Дефицит качественных складских площадей заставил компанию задуматься об автоматизации имеющихся собственных логистических площадок. В данной ситуации решением стала модернизация уже существующих складов путем увеличения их пропускной способности, сокращения издержек на выполнение складских операций и общей производительности работ логистических комплексов. Уникальность данного проекта состояла в многообразии технических решений. Мы постоянно сталкивались с проблемами, требующими неординарного решения. В результате была пересмотрена организация складской логистики и разработана новая складская технология, которая стала возможна благодаря запуску предложенного нами программного обеспечения.
Какими функциональными возможностями обладает программный продукт?
– Мы написали собственную систему управления складом, которая изначально создавалась с учетом специфики мясной отрасли. Это специализированный программный комплекс, позволяющий не только осуществлять учет товара на складе, но и управлять его движением – формировать оптимальные алгоритмы функционирования складского комплекса, беря в расчет топологию склада, параметры оборудования. Образно говоря, такая система позволяет складу не ≪захлебнуться≫ потоком товара и ритмично его ≪переварить≫.
Мясокомбинат «САВА» ведет свою историю с 1998 г. Первоначально объемы производства составляли 500 кг в день. Сейчас мощности предприятия позволяют выпускать в день до 200 т продукции. По объему выпуска продукции компания «САВА» занимает теперь пятое место в России. В настоящее время ее продуктовая линейка насчитывает более 200 единиц разнообразных колбасных и мясных изделий на любой вкус и кошелек. Освоена и мусульманская серия – без добавления свинины. Кроме Башкортостана, продукция поставляется в Татарстан и соседние регионы, а также в Екатеринбург, Тюмень, Москву и страны СНГ: Казахстан и др. Колбасные и мясные изделия под торговой маркой «САВА» – это бренд, означающий высокое качество, широкий ассортимент и соответствие требованиям покупателя. Достигается это благодаря следованию четырем главным принципам: заботе о качестве продукции путем использования передовых технологий, обеспечению порядка и чистоты, эффективной системе управления и ответственности каждого сотрудника. Мясокомбинат «САВА» – предприятие России, где система менеджмента безопасности пищевых продуктов сертифицирована по международным стандартам ИСО 22000-2007 и ХАССП. Это свидетельствует о том, что продукция торговой марки «САВА» безопасна для здоровья и отвечает всем требованиям по качеству.
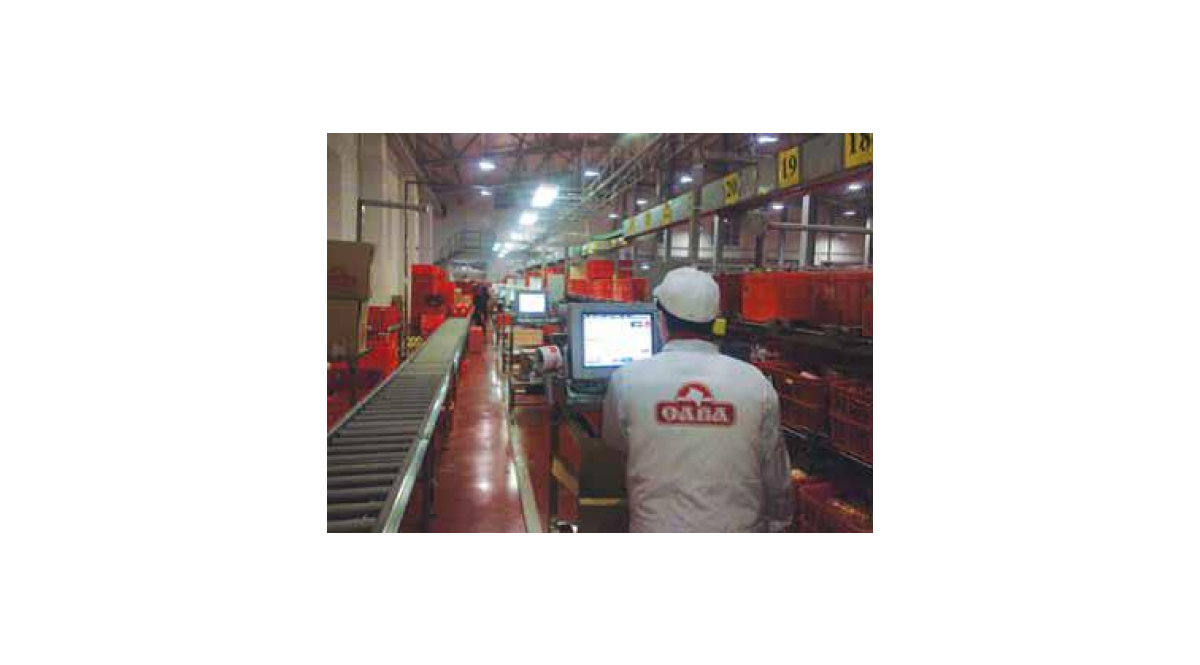
– Внедрение нашей системы управления складом характеризуется полнотой автоматизации процессов: практически все операции, выполняемые на складе, управляются либо контролируются системой. Работа складского комплекса существенно отличается от работы других крупных распределительных центров. В частности, было внедрено наше уникальное решение регистрации данных по готовым колбасным изделиям с использованием радиометки уже на выходе из термокамеры, когда продукт еще находится на раме. Далее продукт поступает на перетарку. До внедрения нашей системы эта операция была узким местом, несмотря на то что выполнялась на восьми точках, занимающих внушительную часть помещения. Сейчас это две точки, способные заполнять до 16 тыс. пластиковых ящиков или гофрокоробов в смену, каждый из которых имеет именную этикетку. Скорость загрузки одного ящика весом 20 кг, включая ввод информации о его содержимом в базу, составляет 5 с. Помимо высвобождения площадей, была упрощена задача перетарки: благодаря регистрации информации о продукте, с рамы заполненный ящик попадает на весы и моментально сканируется одним нажатием, а информация о его содержимом выводится на экран. Повторное нажатие (двойное сканирование) позволяет тут же вывести этикетку. Уникальность автоматизации данного участка склада заключается в возможности регистрации данных об упаковках продукта различного веса в одном ящике, а потом автоматически на основании заложенного в ней оригинального алгоритма программа сама подскажет, где что лежит. Эта гибкость программы дает возможность по требованию клиента формировать необходимый заказ. Еще одно решение – это использование смешанных терминалов сбора данных, что позволяет значительно ускорить весь процесс приема и распределения товара на складе. Мобильные компьютеры собирают идентификационные данные о товаре. Затем эти сведения по сетям передаются в серверную систему, которая обеспечивает доступ к ним в режиме реального времени для улучшения контроля запасов. Специальный модуль включает в себя механизмы анализа свободного складского пространства и определения наилучшего места на складе. Также предусмотрено проведение инвентаризации в любой момент времени. Предоставляется информация о состоянии склада, позволяющая контролировать хранение и поступление сюда продукции. С помощью терминалов сбора данных можно оперативно сформировать заказ или отчет по передвижению товара на складе.
Не менее важную часть автоматизированной системы составляет маркировка товаров и грузов. Решения для мобильной печати позволяют комплектовать товары или помечать упаковки, предназначенные определенным клиентам, специальными наклейками. В сочетании с терминалом сбора данных мобильный принтер этикеток стал очень эффективным решением: маркировка производится на месте, значительно экономится время.
При этом, если возникла проблема с работой принтера, всегда есть возможность возврата информации по этикетированию в нужную точку процесса. Добавлю, что на данном этапе перед нами была дополнительно поставлена еще одна задача: часть продукции должна быть этикетирована на башкирском языке. Мы на это смело подписались и успешно реализовали. Еще одним узким местом склада являлась розничная комплектация заказов. В настоящее время продуктовая линейка мясокомбината насчитывает более 200 единиц разнообразных колбасных и мясных изделий. ежедневно поступает большое количество заявок, на основании которых заказы формируют шесть сотрудников в смену, преимущественно женщины. Раньше это требовало огромных усилий.
Внедрение нашего программного продукта позволило увеличить производительность труда сотрудников участка комплектовки в среднем на 40 % по отношению к ранее существующим показателям за счет оптимизации рабочего места и удобства пользования и обработки информации о заказе.
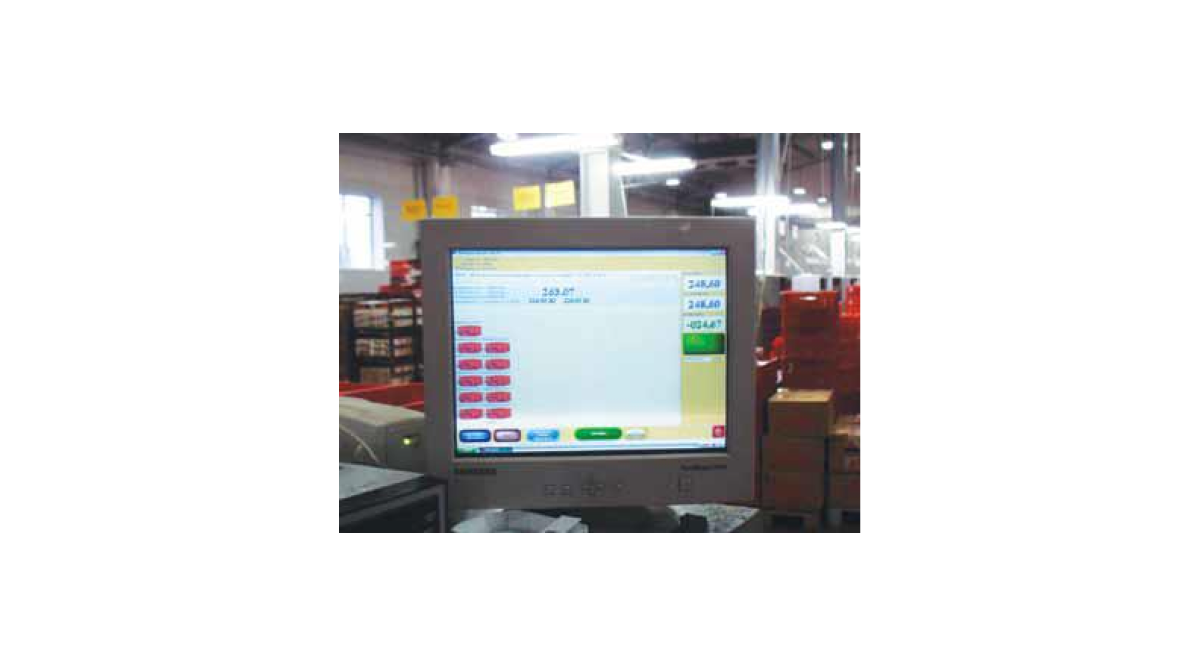
– Благодаря установленной нами автоматизированной системе, контроль осуществляется в каждой точке склада. Всего на складе нами было реализовано около 40 точек учета, причем каждая из них уникальна и выполняет определенную функцию. В результате обеспечивается тотальный контроль над всем процессом с точки зрения выполнения каждой отдельной операции, соблюдения временных и прочих нормативов. Загрузка роботизированного склада продукции выполняется с соблюдением конструктивных особенностей, с учетом рациональности и оптимальности использования склада, на основе анализа АВС. Все это позволяет значительно повысить производительность роботов. Выгрузка со склада осуществляется по внутренним, автоматически сформированным заданиям на основе потребности в отгрузке упакованной продукции конечному клиенту. При формировании заказа партия, подготовленная к отгрузке, дважды проверяется по целому ряду показателей. В памяти программы хранятся и легко выводятся любые данные о клиенте (например, адреса, предложения, графики поставок, выполненные заказы и данные по обороту). По каждому клиенту предусмотрена отдельная матрица. Проводится анализ по недогрузу-перегрузу, отгрузка выполняется с учетом требований по упаковке, времени доставки. Отдельный диагностический модуль в системе выделен для инженерной службы предприятия. С помощью программного обеспечения происходит взаимодействие между всеми подразделениями склада и сменным мастером, который имеет возможность контролировать весь процесс посредством интеграции с видеонаблюдением. Таким образом, реализуется координация, управление и контроль систем комплектации заказов. Кроме того, система осуществляет онлайн контроль за состоянием оборудования, вовремя сигнализируя мастеру участка о проблемных ситуациях.
А.А. Суханов, руководитель склада мясокомбината «САВА»
– Модернизация позволила нам создать по-настоящему умный склад. На сегодняшний день все основные складские процессы, включая приемку, пополнение, набор, инвентаризацию и размещение товара на складе с учетом условий хранения, полностью автоматизированы и контролируются WMS- системой. Кроме того, за счет увеличения пропускной способности склада на 20 % мы имеем возможность обработки большего количества товаров за одинаковый интервал времени, если учитывать ранее существующие показатели. Следует подчеркнуть, что успешное внедрение WMS – не просто дань моде или техническому прогрессу, но и реальное конкурентное преимущество, инструмент оптимизации издержек. Система управления складом позволяет минимизировать влияние человеческого фактора и вероятность совершения ошибок, повысить точность выполнения операций, сформировать оптимальные маршруты передвижения погрузо-разгрузочного оборудования. Как показал опыт мясокомбината «САВА», в результате реализации совместного проекта с компанией «ИСИТ» общая производительность работы склада возросла на 25–30 %, пропускная способность – на 20 %, скорость выполнения заказов – на треть, эффективность использования площади склада – на 20 %.
Но главная идея системы ≪ИСИТ≫ заключается в том, что программа ориентирована на предупреждение возможных ошибок, а не на их выявление в уже готовой продукции. Однако при возникновении спорной ситуации или обнаружении каких-либо несоответствий есть возможность ≪прокрутить≫ весь процесс в обратном направлении и найти причину, возникшую на любой стадии процесса.
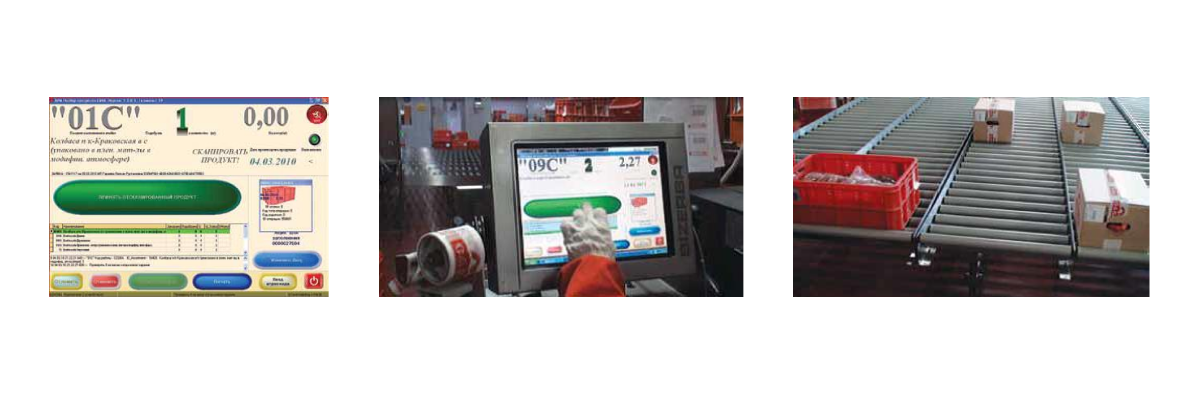
Алексей Николаевич, а как отнеслись сотрудники склада к внедрению системы?
– Период стабилизации длился несколько месяцев, но весь коллектив отлично справился с поставленными перед ним задачами. Особенно наглядны результаты работы комплектовщиков. На каждом участке комплектации в режиме реального времени отслеживается результат работы сотрудника в течение всей смены: что он уже сделал, что делает сейчас. Вообще каждая точка оборудована видеонаблюдением. Хочу отметить, что, прислушавшись к мнению сотрудников, руководство мясокомбината ввело суточный график работы. На каждую смену работник получает задание, выполнив которое он может уйти домой. Это, безусловно, является дополнительным стимулом для работы. Так вот, после внедрения нашей системы суточная норма выполняется за 14–16 ч. Вообще на этом предприятии очень внимательно относятся к сотрудникам, это касается как социальной сферы, так и в создании условий для работы. Поэтому все пожелания непосредственных исполнителей на том или ином рабочем месте были учтены по максимуму. Так, например, сканеры, помимо звукового сигнала, свидетельствующего о регистрации единицы товара, были дополнительно оснащены вибросигналом, что помогает персоналу удостовериться в выполнении действия. На участке розничной комплектации заказов, где, как я уже сказал, работают женщины, было принято решение осуществлять загрузку ящиков весом не более 15 кг. Эти и многие другие нюансы были нами учтены при реализации проекта модернизации на базе системы управления складом. Внедрение WMS-решения привело к тому, что количество допускаемых персоналом ошибок при наборе товара сократилось в два раза. Индивидуально под каждую операцию было предложено и внедрено нестандартное решение. Теперь чрезвычайно широкая ассортиментная группа товаров имеет свой оптимальный технологический процесс размещения, хранения и отбора.
Планируете ли Вы продолжить работу с мясокомбинатом «САВА»?
– Да, мы планируем разработать и реализовать проект по автоматизации производства.
Спасибо за интересную беседу, успехов в работе!
Компания «ИСИТ»